Project Overview
Mark III’s virtual construction, fabrication, and field teams all play a part in saving time and mitigating waste on our projects. On one recent project, in particular, prefabrication nearly cut our construction schedule in half. The electrical team hard at work at a Ross Stores, Inc. distribution center in Shafter, CA, recognized an opportunity to save time and resources through prefabricating multiple door docks and lighting fixtures. Read the story below.
Project Name
Ross CVDC Hotel Conversion
Scope of Work
The project includes a full retrofit of an existing 856K SF Spec Building to meet Ross Stores, Inc.‘s distribution standards. Mark III’s scope includes the demolition of existing power, lighting, service equipment, and feeders. In addition, the project includes the installation and re-routing of existing lighting, power circuits, and other fixtures.
Click here to read the full project scope.
The Approach
Virtual Construction
Our virtual construction team utilized Building Information Modeling (BIM) to coordinate the project prior to construction. At the job site, we used our Trimble robotic total station to layout over 800K SF of lighting in the warehouse.
Prefabrication in the field: A Foreman’s Perspective
On paper, the idea of utilizing manufacturing and lean principles may seem like a piece of cake. But what is it really like from the field perspective?
Jason Tabor, Mark III foreman, says, “We’re doing as much prefab [at Ross] as we can. It helps job productivity and eliminates the chances for materials to be misplaced or lost in the field [especially on a large job site].”
Projects with repeatable units lend themselves to systematic construction processes like prefabrication, allowing for increased efficiency and elimination of waste. While there are many opportunities to gain efficiencies, here are the most common areas of waste:
The 7 sins of waste
- Overproduction
- Waiting
- Transporting
- Inappropriate Processing
- Unnecessary Inventory
- Unnecessary/Excess Movement
- Defects
Repeatability
“Repetition is the mother of learning, the father of action, which makes it the architect of accomplishment.” – Zig Ziglar
Utilizing lean principles and manufacturing has allowed us to reduce waste, therefore allowing owners to build more with less. Through the standardization of design and shift to manufacturing, Mark III has been able to constitute a delivery method that treats buildings as products rather than projects.
Here’s a closer look at how standardized and repeatable units were leveraged to save time and money in the field.
Door Docks
This project included 49 identical door docks. In order to save time and capitalize on the repetitive nature of these units, we decided to kit the electrical installation for each door. Kitting is the process of supplying individual parts and tools for a task that are grouped, packaged, and shipped together as one custom unit to a point of use area.
The electrical needed for each door was cut, threaded, and packaged into a complete kit. These kits were placed by each door dock, ready to be installed when the field team was ready. This eliminated the need to travel across the site in order to access the necessary materials and equipment.
Knowing the exact dimensions of the doors allowed our field and manufacturing team to cut and thread all of the necessary rigid conduits at once, rather than on a door-by-door basis. The project foreman, Jason Tabor, explains, “We spent approximately 40 minutes [prefabbing, kitting and installing] each door compared to the approximately 70 minutes it would have taken to install each door on-site without prefabbed and kitted material. I expect our labor hours to decrease as we move forward as I believe we have overcome the learning curve and will only excel from here on out.”
Time Savings
30 minutes per door
42.8% savings for the task
Light Fixtures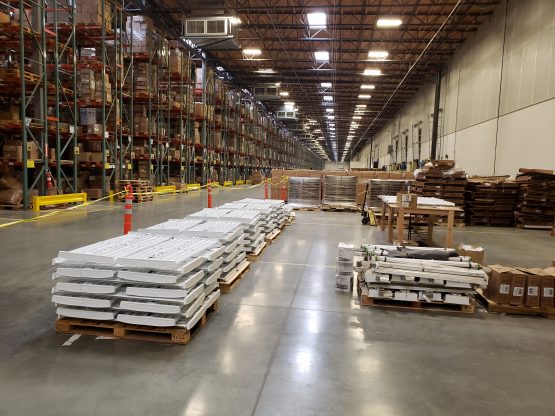
This project also included the installation of 440 light fixtures. Installing the lights required multiple steps: unpacking the fixture, adding the hanger kit, pig-tailing the ballast wires for a single termination point, and stabbing in the M/C connectors into the fixture. Manufacturing the fixtures in a controlled environment allowed our team to complete each unit in just 6 minutes compared to the 14 minutes it typically takes to build one-by-one in the field on a lift.
Prefabrication of these lights also decreased the likelihood that material was lost or scattered throughout the job site. This meant a decrease in wasted material and time and a safer work environment.
Time Savings
8 minutes per unit
57.14% savings for the task
Conclusion
By prefabricating and manufacturing door docks and light fixtures in a controlled environment, our team was able to maximize efficiency and reduce hours by 45.23% on the Ross job. Way to go team!
To learn more about our manufacturing capabilities, check out our website or contact us!